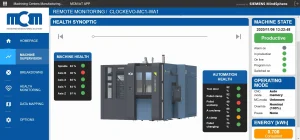
PREDICTIVE MAINTENANCE ON CLOUD MINDSPHERE
On the occasion of the BI-MU fair in Milan, MCE presented a new and interesting application, concerning Predictive Maintenance on Cloud MindSphere, developed on the cloud platform in collaboration with the 40Factory company. PREDICTIVE MAINTENANCE ON CLOUD MINDSPHERE: